How 3D Printing is Shaping a Sustainable Future in Manufacturing

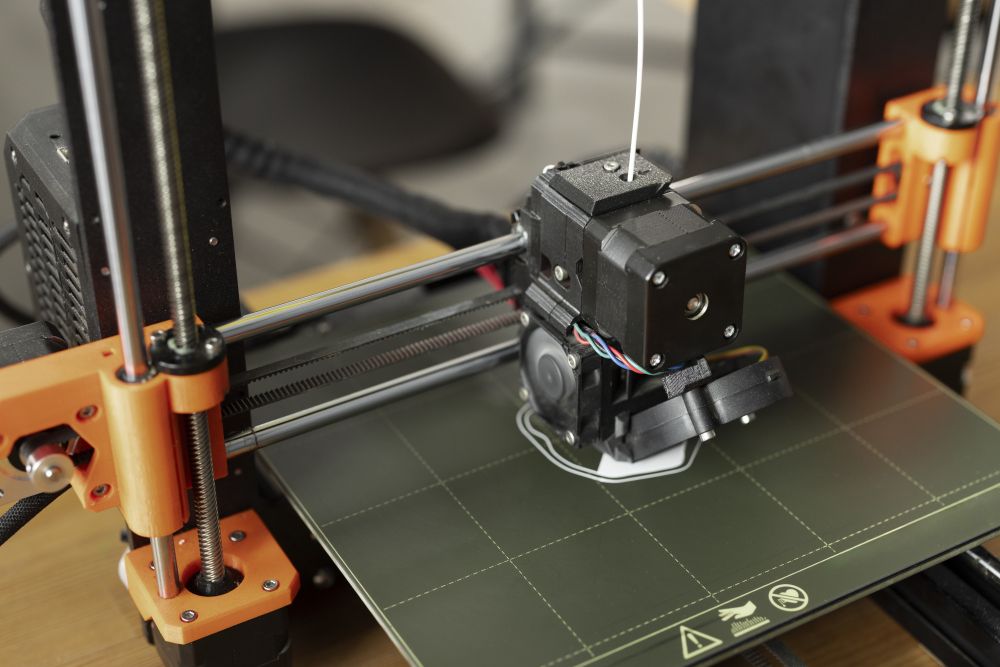
Cut through the green tape
We don't push agendas. At Net Zero Compare, we cut through the hype and fear to deliver the straightforward facts you need for making informed decisions on green products and services. Whether motivated by compliance, customer demands, or a real passion for the environment, you’re welcome here. We provide reliable information—why you seek it is not our concern.
Introduction to 3D Printing and Its Role in Sustainability
3D printing, also known as additive manufacturing, is a process that creates three-dimensional objects by layering material based on a digital model. Unlike traditional manufacturing, which often involves cutting or moulding raw materials into desired shapes (subtractive manufacturing), 3D printing builds objects layer by layer using only the material required. This method is precise, efficient, and versatile, allowing manufacturers to create complex geometries that would be difficult or impossible using traditional techniques.
3D printing has the potential to radically change the way we approach manufacturing, particularly when it comes to sustainability. Traditional methods often result in excess waste, inefficiencies in material use, and high carbon emissions due to transportation and logistics. By contrast, 3D printing can help reduce waste, promote localized production, and create parts with less energy and resources, making it an ideal technology for sustainable manufacturing practices.
Traditional Manufacturing and Material Waste
In traditional manufacturing, many processes are subtractive, meaning the material is removed from a larger block to create the final product. For example, machining or milling processes can result in a significant percentage of the original material being wasted as scrap. Injection moulding requires the production of moulds, which can only be used for a limited time and create excess material through trimming and rejects. These methods often lead to inefficiencies, contributing to higher costs, excess waste, and greater environmental impact.
3D Printing as an Additive Process
In contrast, 3D printing’s additive approach uses only the material necessary to build an object. This reduces waste because no excess material is removed or discarded in the process. This makes 3D printing not only more efficient but also more environmentally friendly.
Localized Production: Reducing Transportation and Carbon Emissions
One of the most significant environmental advantages of 3D printing is its ability to facilitate localized production. Traditional manufacturing often relies on large, centralized factories that produce goods in bulk and ship them across the globe. This globalized model necessitates long-distance transportation via ships, trucks, and planes, which contributes to significant carbon emissions.
With 3D printing, products can be manufactured closer to where they are needed, minimizing the reliance on global supply chains. This decentralized production model reduces the need for extensive transportation networks, thus lowering fuel consumption and the associated emissions. For instance, instead of manufacturing a component in one country and shipping it to another, companies can set up localized 3D printing facilities that produce parts on demand near the point of consumption. This cuts down on transportation costs, delivery times, and the environmental impact of long-haul logistics.
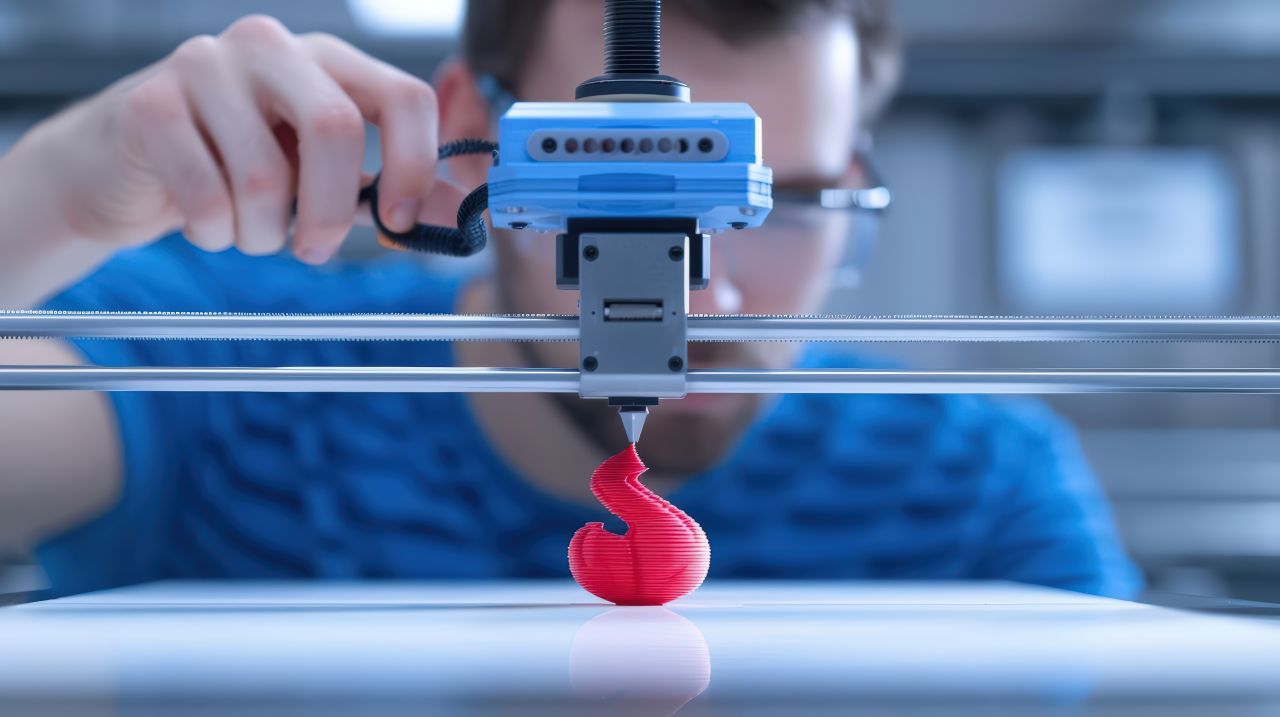
On-Demand Manufacturing: Reducing Excess Inventory and Waste
In traditional manufacturing, companies often produce goods in large quantities to meet anticipated demand, leading to overproduction and the accumulation of excess inventory. This model is not only resource-intensive but also creates waste when products go unsold or become obsolete before they can be used.
3D printing, by contrast, enables on-demand manufacturing, where products are made only when they are needed.
Benefits of On-Demand Manufacturing
Customization: 3D printing allows manufacturers to create custom parts and products on a per-order basis. For instance, in the medical industry, custom prosthetics and dental implants are made for individual patients rather than mass-produced in bulk.
Reduced Storage Needs: By producing items only when needed, companies can dramatically reduce the space and resources required for storage. Warehouses filled with unsold goods become unnecessary, contributing to cost savings and sustainability.
Lower Risk of Obsolescence: On-demand manufacturing reduces the risk of producing items that may become outdated before they are sold. Instead of stockpiling large quantities, products can be updated and printed as new designs or technologies become available.
Industries Where 3D Printing Reduces Waste
Aerospace: In aerospace manufacturing, where lightweight and durable parts are critical, 3D printing has enabled the production of highly efficient components with minimal waste. Boeing, for example, uses 3D printing to create parts for its aircraft, reducing material usage and weight, which in turn cuts fuel consumption and carbon emissions during flights.
Automotive: The automotive industry has adopted 3D printing for both prototyping and production. Ford and BMW, for instance, use 3D printing to create lighter, customized parts that reduce material waste and improve overall vehicle efficiency.
Medical: In the medical field, 3D printing is used to create custom prosthetics, implants, and surgical tools. These products are tailored to individual patients, minimizing waste by eliminating the need for mass-produced, one-size-fits-all solutions.
Development of bioplastics and other eco-friendly materials
The development of bioplastics and other eco-friendly materials in the 3D printing industry is a key step toward sustainable production. Bioplastics are derived from renewable sources like corn starch, sugarcane, or algae, and they offer an environmentally friendly alternative to traditional petroleum-based plastics. These materials are biodegradable, reducing long-term waste and environmental impact.
In addition to bioplastics, researchers are exploring recycled plastics, where used materials are repurposed into 3D printing filaments, contributing to a circular economy. Innovations like carbon-fibre-reinforced composites and plant-based resins are also gaining traction, offering both sustainability and strength for industrial applications.
Energy Consumption in Traditional Manufacturing
Traditional manufacturing processes, like CNC machining (subtractive) or injection moulding, are often energy-intensive due to several factors:
Subtractive methods require more raw materials and energy to process excess material, leading to waste.
Injection moulding, for example, involves heating plastic resins and using large presses, which consume significant energy, especially for mass production.
These methods are optimized for large-scale production, which means high energy usage when producing goods in bulk.
While these processes are efficient for mass production, they tend to consume more energy when producing small batches or highly customized parts due to machine setup, mould creation, and high operational loads.
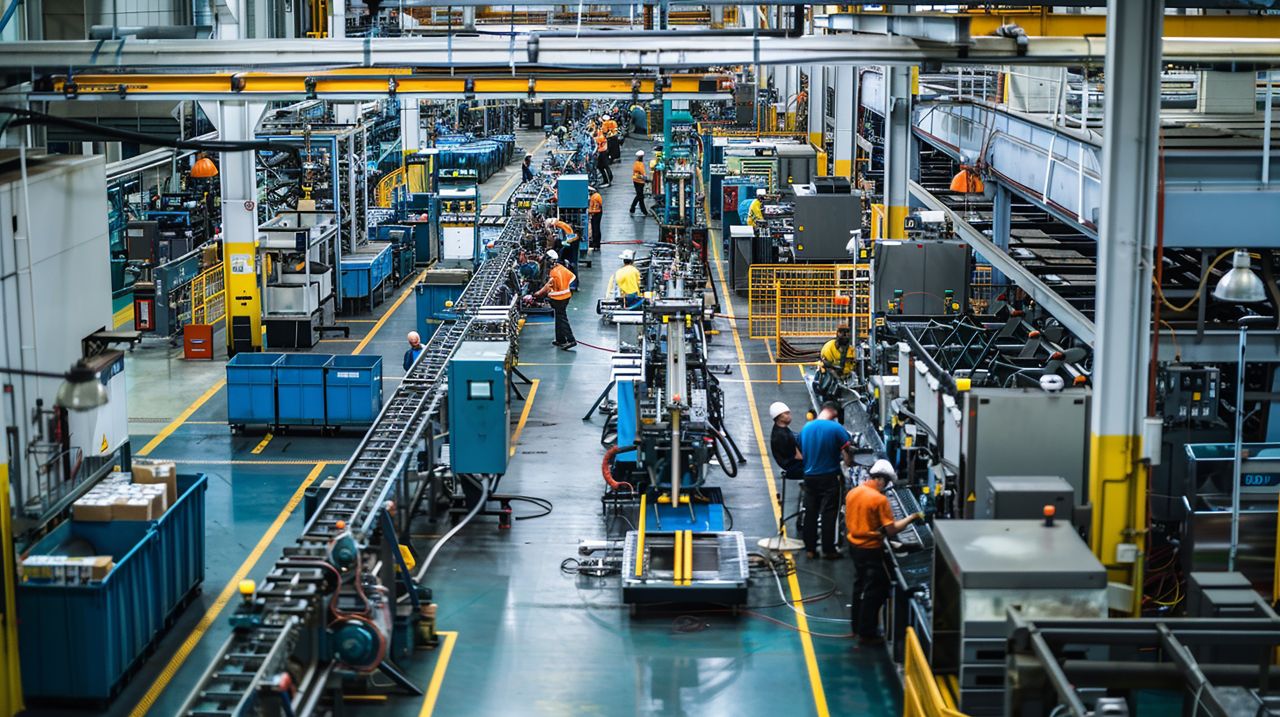
Energy Consumption in 3D Printing
3D printing's energy consumption can vary based on the technology used (e.g., FDM, SLA, SLS), but it generally offers more energy efficiency in several ways:
3D printing uses only the necessary material to build a part layer by layer, reducing waste and the energy required to manage excess material.
Unlike traditional methods that require moulds or cutting tools, 3D printing eliminates the need for energy-intensive setup processes.
3D printers can produce items in small batches with minimal energy input, making them ideal for custom, low-volume production. Energy consumption is often proportional to the complexity of the design, rather than the scale of production.
Key Comparisons
For Small Batches and Prototyping:
3D printing is generally more energy-efficient than traditional methods for low-volume production or rapid prototyping, as it avoids the energy-intensive setup and material waste of traditional manufacturing.For Mass Production:
Traditional manufacturing methods, particularly injection moulding, may consume less energy per unit in mass production scenarios. This is because once moulds and machines are set up, they can produce large quantities at high speed with lower per-unit energy costs, whereas 3D printing, depending on the technology, may take longer and use more energy per unit.Material-Specific Energy Use:
Some 3D printing technologies, like laser sintering or metal 3D printing, require high temperatures or powerful lasers, which can increase energy consumption. However, innovations in these fields are continuously improving efficiency.
Energy Efficiency Potential
While 3D printing may consume more energy in certain applications, particularly for high-energy processes like metal printing, its ability to reduce waste, minimize transportation, and promote on-demand manufacturing offsets some of this. Additionally, ongoing research into improving energy efficiency in 3D printers, such as low-energy printers and sustainable materials, is helping reduce the overall energy footprint of the technology.
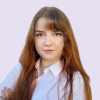
More related content
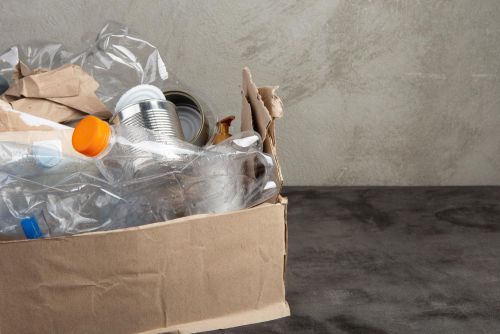
Extended Producer Responsibility (EPR) for Packaging: Country-by-Co...
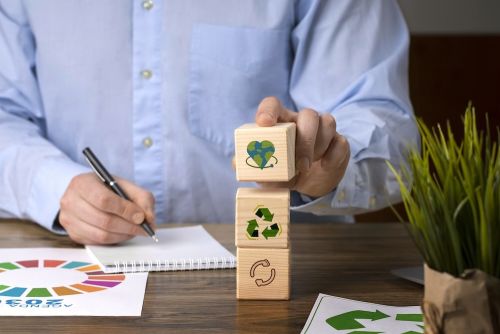
What Is Scope 3? Understanding Indirect Emissions and Their Regulat...

The EU's Omnibus Proposal: A Deep Dive
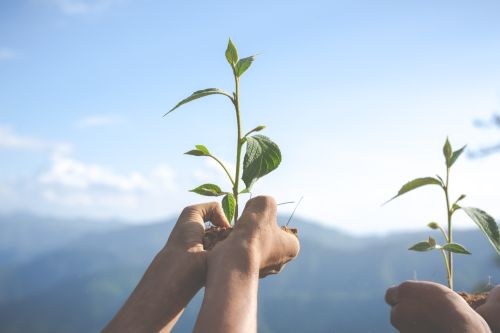